康尼电子围绕三年计划和六年规划研讨会提出的生产效率提升战略目标和工作计划,以全价值链理念为牵引,以自动化改造和工序整合优化为抓手,推动制造运维中心效率持续提升和制费不断下降。为使此项工作尽快落地并及时显现效益,生产部对线束车间布局进行重新规划调整,优化车间布局,精益化物流路径。
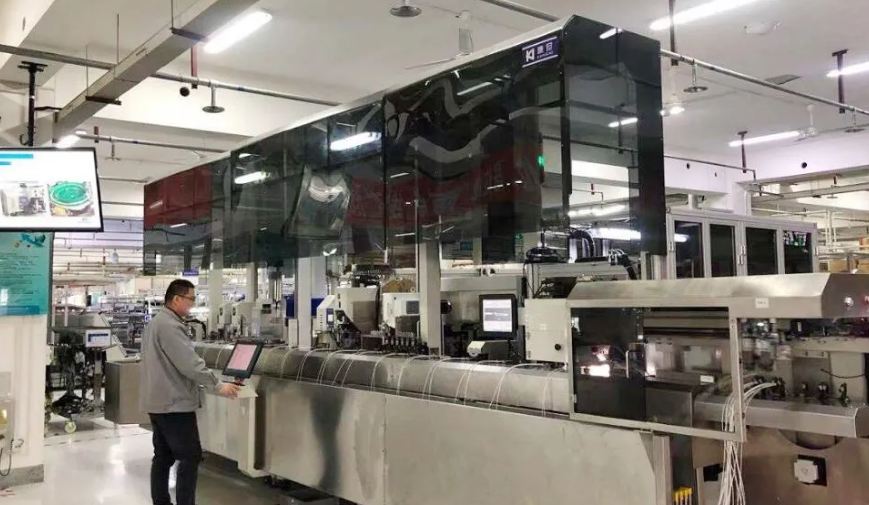
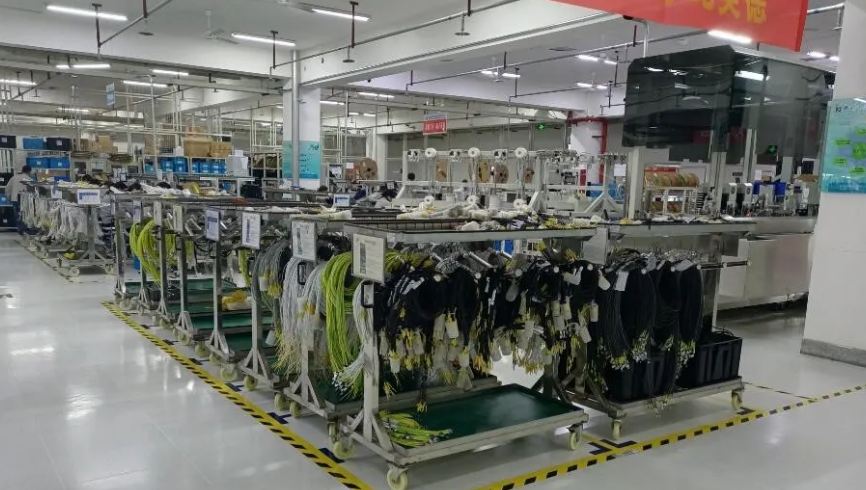
针对单芯线一体化加工设备原材料、半成品建立了单芯线半成品超市,规划了方便由仓库直接配送的物流路径。单芯线的加工由原先3个分散、独立的生产单元合并为1个集中的生产单元。单芯线生产效率由43秒/根降低至约8秒/根,效率提升约80%,生产周期由16小时/列车缩短约60%至7小时/列车左右。
部件组装生产单元合并为2个涵盖组装和检验的生产单元。组装产品的周转次数由2次减少为1次,平均缩短各工序产品搬运距离约8米,有效提升了产品周转效率和作业效率。
为解决分散布局、长距离搬运导致的作业效率低、生产周期长、库存品多等问题,此次建立了2条集成预加工、总装和检验功能的总装线体。优化后,通过流水作业,产品生产周期由14小时/列车缩短至约6小时/列车;产品周转次数由3次缩短至1次。
未来,康尼电子将继续挖掘识别精益改善机会,依据产品结构BOM和自动化导入进程,持续优化布局,不断提升生产效率和产品品质。